
SERIE: los autores de The Power of Process abren su nueva serie explicando por qué es fundamental integrar el desarrollo de productos y procesos.
Palabras: Eric Ethington y Matt Zayko
“Todos los males de la organización aparecen en la planta de producción”. Juan Sacudió
¡HUELGA DE MARY SHELLEY!
Como nuevo administrador del sitio, estaba tratando de ser respetuoso con lo que estaba viendo. Había aprendido mucho antes que siempre había una razón por la que las cosas eran como eran. Quizás no sea una gran razón, pero una razón que tenía sentido en ese momento. Luego entré en la sala de producción de bombas con control ambiental. Se había instalado recientemente y se promocionaba como lo último en Lean Thinking. En realidad, fue un proceso de "Frankenstein": un montón de conceptos esbeltos unidos.
Era un flujo de una sola pieza, hasta llegar a los amortiguadores giratorios de seis piezas entre cada estación. Sí, girando en círculos sobre platos giratorios. No tenía sillas, pero no había tiempo de máquina para permitir que los operadores se trasladaran a otra operación. Tuvieron que estar allí todo el día como si estuvieran haciendo guardia afuera del Palacio de Buckingham. La celda tenía forma de U, pero era difícil aprovechar esta configuración; su único impacto fue hacer que la entrega de material fuera un desafío. Y así comenzó el trabajo de recopilar datos de movimiento, datos de máquinas y otra información de procesos para reconfigurar este intento bien intencionado y convertirlo en algo mejor.

LENTES PARA VER MEJOR
Nuestro libro reciente, The Power of Process , presentó los marcos específicos (6CON) para que las personas analicen y diseñen adecuadamente un nuevo proceso mientras optimizan los recursos de creación de valor. El marco es aplicable a la creación de cualquier proceso que involucre personas, tecnología o equipos, ya sea que la aplicación sea en manufactura, atención médica, servicios, comercio minorista o cualquier otra industria. Este marco puede dar como resultado una mejora del 30-50 % en seguridad, calidad a la primera, tiempo de entrega del cliente, eficiencia de capital, productividad laboral, espacio de piso y más que podría sumar millones de dólares por año y un retorno de la inversión 10 veces mayor.
En los próximos meses, publicaremos una serie de artículos centrados en los seis marcos que componen el modelo 6CON: contexto, conceptos, convergencia, configuración, confirmación y mejora continua. Este artículo inicial nos ayuda a presentar el caso de negocios para la importante integración del desarrollo de productos y procesos.

Al escribir el libro, discutimos cómo contar mejor la historia para compartir de manera efectiva la interacción del sistema social y técnico que es necesaria para lograr una creación de procesos verdaderamente grandiosa. Nos decidimos por un producto industrial (interruptor de alto voltaje) que se construye en un entorno de fabricación, y basamos la historia en un ejemplo de la vida real. Una de las razones por las que elegimos el interruptor de alto voltaje es que es un producto físico y tangible que es más fácil de imaginar para el lector, incluso si no pertenece a una organización basada en productos o fabricación. Su "producto" puede ser una vía clínica para el paciente, una experiencia de cliente minorista u otra actividad.
CUESTIONES DE FABRICACIÓN
Pero una razón más importante por la que elegimos este ejemplo es que la fabricación sigue siendo un enorme impulsor del poder económico, a pesar de su papel disminuido en muchos países desarrollados en las últimas décadas. En los Estados Unidos, la industria manufacturera por sí sola representaría la octava economía más grande del mundo. El gasto en investigación y desarrollo (I+D) en los EE. UU. en fabricación y procesos es de casi 300 000 millones de dólares anuales, con otros 200 000 millones de dólares gastados en nuevos equipos de capital para la fabricación y casi 60 000 millones de dólares en instalaciones para todos los equipos. Más de 12 millones de personas están empleadas en la industria manufacturera de EE. UU., incluidos casi 1 millón de ingenieros, el 25 % del total de ingenieros del país. La mayoría de las empresas de todo el mundo gastan entre el 3 % y el 15 % de sus ingresos anuales en inversión en I+D. Adicionalmente,
Sin embargo, a pesar de la creciente inversión en personas y recursos de capital para los procesos de fabricación en todo el mundo, la mayoría de las organizaciones no tienen un enfoque estándar para crear nuevos procesos. Esto da como resultado un gasto excesivo en capital y trabajo manual excesivo en el rango de 30 a 50 % (según nuestros más de 25 años de experiencia, estimamos que menos del 10 % de las organizaciones tienen un enfoque estándar para el diseño de procesos lean que está integrado con el desarrollo de nuevos productos).
ESTA EN LOS DETALLES
Cuando profundizamos, encontramos una falta básica de comprensión por parte de quienes diseñan el nuevo proceso. A veces se han calculado los tiempos de ciclo y su relación con un tiempo takt, pero la mayoría de las veces no. Cuando comenzamos a cuestionar los rendimientos proyectados, los tiempos de cambio, el tamaño de los lotes, las rutas de movimiento y las opciones de equilibrio, la información se vuelve aún más confusa. Esencialmente, la organización y sus gerentes están a punto de gastar una cantidad significativa de dinero en capital, pero solo tienen una vaga comprensión de por qué. Una vez más, esto es normal y seguirá siendo normal porque nadie pregunta al final, "¿obtuvimos el valor de nuestro dinero o logramos nuestro objetivo?" Se puede analizar un número financiero general, o tal vez el momento del lanzamiento, pero ¿con qué frecuencia se identifican y comparten las causas reales de cualquier variación para el aprendizaje? Generalmente nunca.
Dada esta actividad de desarrollo de procesos inicial limitada, existe una necesidad crítica de cambiar el enfoque para crear nuevos flujos de valor y procesos, y una excelente manera de realizar esta necesidad es a través del poder de la narración. Hay muchas personas inteligentes y bien intencionadas que, año tras año, crean procesos que están cargados de problemas tan pronto como se inician. 6CON es una práctica desarrollada, no un conjunto de herramientas, para mover el desarrollo de procesos de una organización de decisiones individuales a un enfoque holístico. Y dado que el 70% o más del costo de un producto o servicio generalmente se fija una vez que se seleccionan los diseños, es una gran ventaja competitiva para las pocas empresas que han descubierto esto.
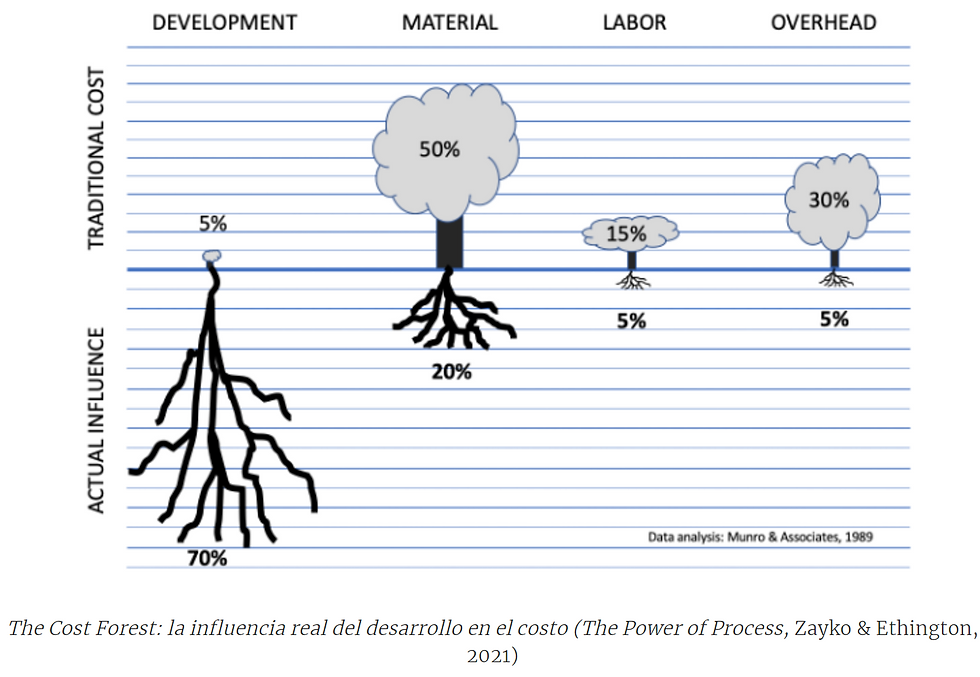
El poder del proceso está escrito para conectar una transformación realista con los desafíos técnicos detallados, así como la participación de las partes interesadas, cada una con sus propios sesgos. Los puntos clave y las acciones obligatorias se ofrecen a lo largo del libro para reforzar el aprendizaje de lo específico a lo general. En el caso de estudio, un equipo de trabajo empoderado se encarga de desarrollar una sola línea de producción para un nuevo producto. A medida que se desarrolla la historia, crean un proceso mejorado que ahorra $5,6 millones (recuperación de 9x) durante el corto ciclo de vida del producto, así como otros beneficios medibles en calidad, ergonomía y entrega. Para un beneficio aún mayor, establecen una nueva forma de trabajar e involucrar a las personas que se puede aplicar a todas las actividades futuras de creación de procesos para minimizar el "touzen" posterior al lanzamiento: el retrabajo que ocurre con los procesos mal diseñados.
Para hacer correctamente este trabajo de desarrollo inicial y crear un proceso Lean sólido, uno tiene que enfrentarse a la complejidad de la colaboración requerida y al escepticismo de mejora continua que las personas aportarán a un proyecto, debido a sus malas experiencias pasadas. Nuestro objetivo es compartir el pensamiento dentro de cada uno de los marcos de 6CON y detrás de los conceptos para demostrar la lógica por la cual uno podría derivar su propio enfoque situacional, un enfoque atractivo que mejorará el valor y evitará el desperdicio en primer lugar.
NUESTRA LLAMADA DE ALERTA
Para volver a la historia que abrió este artículo, tenga en cuenta que esto no es un gran ejemplo de creación de procesos lean, pero uno de kaizen que no debería haber sido necesario si se hubiera diseñado el proceso correcto para empezar. Con atención a los detalles del proceso, la celda se reconfiguró de seis estaciones primarias a nueve estaciones equilibradas con uno o dos segundos de diferencia. Esto significó que agregamos tres personas a la operación, pero la productividad, medida en piezas por persona por hora, aumentó en un 85%. Se desacoplaron dos procesos de alimentación que estaban conectados directamente a la parte posterior de la celda original y se estableció un pequeño supermercado. Agregamos inventario, pero con cierta simplificación de las estaciones de sub ensamblaje, el equipo ahora podía alimentar dos celdas de ensamblaje en lugar de una. El aumento de la productividad nos permitió renunciar a la compra de una celda más, reduciendo la inversión en un 40%.

Para citar a Deming, "Un mal sistema siempre vencerá a una buena persona". Grandes personas diseñaron la primera iteración de este proceso y grandes personas aprendieron y rediseñaron el proceso mejorado, pero si no hubiéramos reflexionado y preguntado cómo podríamos evitar esta situación en el futuro, habríamos seguido atrapados en el juego de reelaboración. Tuvimos nuestra “llamada de atención”. La siguiente decisión fue nuestra.
Acerca del autor.
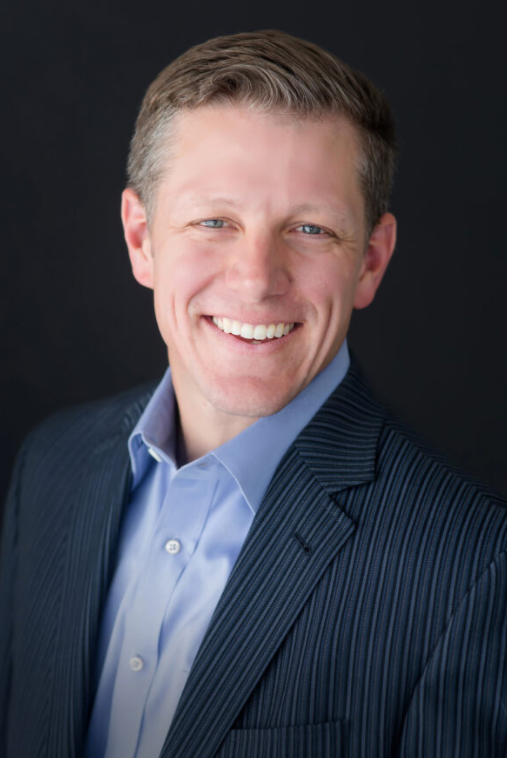
Matt Zayko es líder Lean en GE Hitachi Nuclear Energy

Eric Ethington es Entrenador sénior de Lean y Gerente de Programa, Desarrollo de Procesos y Productos Lean, en el Lean Enterprise Institute.
TRANSCRIPCIÓN: Areli Álvarez Lean Construction México®